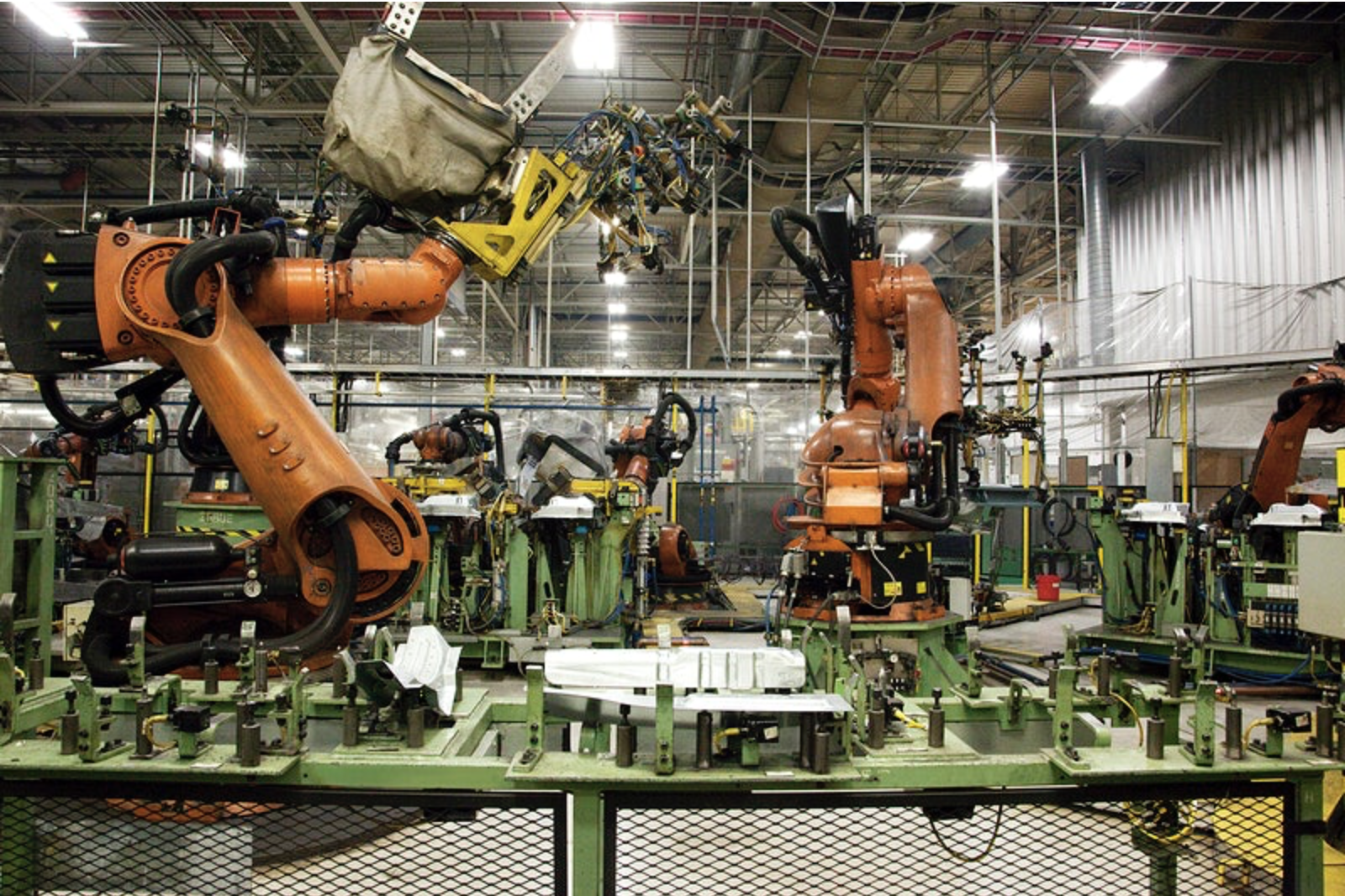
IHS Markit’s Purchasing Managers’ Index (PMI) fell to the lowest rate ever of 33.4 for April since the index began in July 1997, down from 44.5 in March. A score below 50 indicates contraction. The last lowest score was in November 2008; manufacturing has been here before.
Shock
The sector has been suffering the double whammy of ‘demand shock’ with sales orders declining in around 80% of all manufacturing companies together with spikes in certain sectors like medical, food and beverages, alongside ‘supply shock’, as evidenced by an inability to locally source parts.
Manufacturers, while exempt from lockdown, have not furloughed as deeply as other sectors. They are having to manage liquidity issues like never before, in the context of inflated wage pools and the greater level of capital intensity employed in order to remain competitive, especially since 2008.
Two great global initiatives appear to be intermingling. Chinese domination of global manufacturing and Western economy re-adjustment to a more advanced manufacturing paradigm.
China Syndrome
China is the major global manufacturing power in all sectors, including automotive, consumer, electronics and pharma/medical as well as a generic supplier of critical raw materials, components and sub-assemblies.
Traditionally, UK executives have considered China’s advantageous position on cost, quality and overall high level of agility to fulfil ‘ramp-ups’ to demand as major advantages. On this risk matrix, China was viewed as ‘safe’ and controllable in comparison to other regions such as North Africa or the Middle East, for example, when skewed by geopolitics. The recent crisis has shown that global events may literally ‘Trump’ traditional thinking.
Supply chains take an awful lot of finessing to establish and maintain so any re-adjustment programme will need to look much harder at resilience, configuration and load balancing between multiple locations. These type of review processes take time but there is evidence that it was already changing.
It was changing before Covid-19
The UK scenario was one of post-Brexit investments delays, declining market performance in key sectors such as automotive, a requirement to embrace digitisation and overall lowering of sales margins. Manufacturing was in need of a boost and global geopolitical conditions were starting to change.
Prior to the pandemic, the US was clearly leading in the drive to change the equilibrium, actively challenging China’s dominance. There had been a reversal in the US 2019 reshoring index, hot on the heels of a burgeoning trade war with newly imposed tariffs on Chinese products. This was supplemented by accusations of unfair trading, intellectual property theft and national security, particularly with a focus on Huawei and 5G technologies.
Practically speaking, firms were questioning was China even a ‘low cost country’ anymore? With longer lead times than locally based production, worsening product quality due to staff retention issues as wages skyrocketed, some supply chains were struggling to find the significant costs savings anticipated. Could the traditional paradigm be trusted?
As the pandemic impact was felt, Japan was one of the first countries to react, flicking the ‘switch’ by offering a 240 billion-yen ($2 billion) incentive for companies shifting production back to Japan or diversifying to another country in South East Asia.
Readjustment, Resilience, Remodelling
In the short term it is expected that the impact of Covid-19 will be similar to 2008. Costs may not reduce in line with the lower levels of sales performance expected and margins could be heavily impacted as a result, way beyond the previously seen average downturns of 50% and into the red.
It is vital that companies heed the warning and live in the reality of this re-adjustment by ‘right sizing’ their operations.
This means focusing on core activities, controlling costs and managing elements of their marketing mix they may not have been traditionally comfortable with such as; pricing readjustments, re-negotiation of long-term supply agreements or even moves to vertically integrate with their key customers or suppliers.
In the medium term, refreshing international supply chains to make businesses more resilient should become critical to risk management. There will likely be increasing use of technology to shrink distance/sharpen communication, greater transparency of supplier production metrics and more critical demand modelling.
Longer term, a ‘local’ mentality may prevail with greater levels of collaboration with government combined with a higher level of reshoring. This level of remodelling could have a dramatic impact on the manufacturing sector and the UK economy.
For now, though, survival is the challenge, just like 2008.
If you’d like to discuss this blog post or share your own perspective on the issues covered, please get in touch or comment via our social media channels on LinkedIn or Twitter.
Established in 2012, Whitecap Consulting is a regional strategy consultancy headquartered in Leeds, with offices in Manchester, Milton Keynes, Birmingham, Bristol and Newcastle. We typically work with boards, executives and investors of predominantly mid-sized organisations with a turnover of c£10m-£300m, helping clients analyse, develop and implement growth strategies. Also, we work with clients across a range of sectors including Financial Services, Technology, FinTech, Outsourcing, Consumer and Retail, Property, Healthcare, Higher Education, Manufacturing and Professional Services, including Corporate Finance and PE.